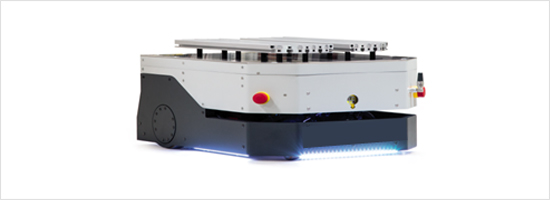
Specifications | Dimensions : L=860mm, W=600mm, H=355mm |
---|---|
Stacking Capacity : Max.500kg | |
Speed : Max.1.5m/s | |
Positional Accuracy : +/-10mm | |
Stroke : Optional | |
Navigation : SLAM, inductive/RFID, optical/RFID | |
Communication : WLAN |
AGV (Automated Guided Vehicle)
is a railless, unmanned transfer vehicle that is driven based on autonomously programmed instructions based on inducing signals
of magnetic field, optics, laser and electromagnetic field, without physical rails or inducing structures on the floor.
AGV is equipment that allows for transport and assembly of new parts and addition of production process by more flexibly adding or removing production processes
as needed without redesigning the entire production process.
We promise the most efficient and optimized system suitable for the field conditions.
Productivity is improved because it can be used flexibly
without restriction of routes such as existing facilities.
It ensures technician’s safety by preventing collisions
by using safety detection sensors while transporting heavy goods.
Flexibility is improved by adding or deleting processes such as assembly
and production without redesigning.
Specifications | Dimensions : L=860mm, W=600mm, H=355mm |
---|---|
Stacking Capacity : Max.500kg | |
Speed : Max.1.5m/s | |
Positional Accuracy : +/-10mm | |
Stroke : Optional | |
Navigation : SLAM, inductive/RFID, optical/RFID | |
Communication : WLAN |
Specifications | Dimensions : L=1000mm, W=850mm, H=900mm |
---|---|
Stacking Capacity : Max.10kg | |
Speed : Max.1m/s | |
Positional Accuracy : +/-2mm | |
Navigation : inductive/RFID, optical/RFID transponder, gyro sensor, QR code |
|
Communication : WLAN |